SUEZ site-seeing | Part 6 | Solid Recovered Fuel (SRF)
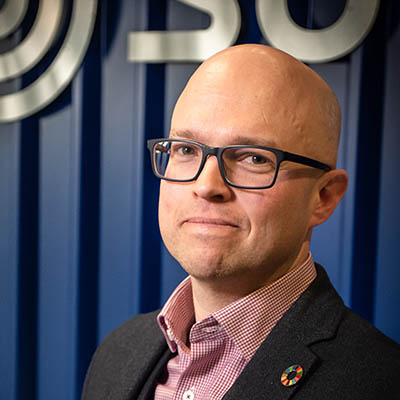
In the run up to Christmas 2017, I was out and about visiting SUEZ’s sites with stops at Avonmouth materials recycling facility (MRF), Severnside Energy Recovery Centre, rail based transfer stations in West London, the new Eco Park development in Surrey, and community recycling centre and re-use centre in Leatherhead.
In anticipation of my next batch of site visits, where I will be joined by SUEZ’s Chief Operating Officer – Business Development, Graham Mayes, I decided to get to know the sites closer to my home, in the Midlands.
In recent weeks, I visited Malpass Farm, (SUEZ’s Solid Recovered Fuel (SRF) facility in Rugby), Packington the closed landfill site in Coventry, and our materials recycling facility (MRF) at Landor Street (Birmingham).
Malpass Farm – baking SRF cake
January 2018 has started with a flurry of activity, it seemed only right that the first of the next batch of visits should happen at the site I call home, at Malpass Farm in Rugby. The site is home to the company’s premier solid recovered fuel (SRF) production line, where SRF is produced as a substitute for coal to fuel the local cement works, CEMEX.
I remember being told on my very first day at the site “it is all about the cake mix” and now this makes perfect sense. If the wrong ingredients are added, you can’t bake the cake you want. Malpass Farm is a production site where materials are input at one end , and processed to create another material at the other end – the crucial part of the process is that the output material needs to meet very specific customer demands.
Partnership
This site operates in partnership with CEMEX, a concrete manufacturer that is located next door. Based on a 25-year relationship CEMEX is the principal off-taker for the SRF produced here (currently the company receives 140,000 tonnes annually).
The site was opened in September 2015, and can handle 180,000 tonnes of mixed residual waste – 80% of this is from industrial and commercial sources and 20% from regional municipal collections. The materials used are largely by-products from other regionally based treatment and recovery facilities, and as such support the circular economy concept. The business case for the site is simple: we are saving money on treatment and landfill costs, whilst CEMEX is reducing their environmental impacts and reducing their use of fossil fuels.
This site is primarily a production facility, and given the exact specification of the SRF needed by CEMEX, controlling what comes in to the site is critical to winning the battle against rising handling costs. Since opening, the site has dealt with as many as 50 different customers (almost all commercial) in terms of feedstock provision into the SRF facility, but over time they have reduced the customers down to 18 or so, each delivering the feedstock quality. The materials input are specifically chosen to reduce chlorine levels from PVC and ensure consistency in calorific value and moisture and frequency.
Over the two years of operation the site has improved its ability to sample input streams and identify customers who have poorer quality feedstocks. SUEZ then works with them, feeding back on what the issue is and establishing how they can improve the quality of the materials coming on to the site.
Each load of incoming material is visually checked by a quality controller to ensure it follows the material acceptance criteria agreed with each supplier. Many of the key sources of feedstock now deliver loads that are 75% suitable (or better), but some are as low as 45% and these suppliers are now the focus of the customer engagement team.
So how does the plant work?
The process is simple, but effective.
First the materials enter the bag shredder to free the input materials, where they go through the first shredder to break the materials down into smaller pieces. The trommel further helps to segregate materials by size, enabling the right materials to make it through to SRF production eliminating the fines and the oversized items. The target materials are in the range 40-300mm and the wind shifter further helps separate light from heavy, with the heavy fraction joining the oversized items separated earlier. Over-band magnets and eddy current separators enable any metals and aluminium to be extracted from the SRF materials.
Next up, the optical sorter can identify PVC by infrared refraction and a jet of air removes any unwanted items. PVC is the main source of chlorine in SRF and chlorine content is a crucial parameter to determine if solid recovered fuel can be used as a substitute to coal in the cement industry, therefore it must stay beneath 0.8%. The final shredders ensure the material for the SRF mix is at 30mm – the desired grade.
The analyser is a live quality control system, 10% of the final SRF material passes through it each day to monitor the quality of the product. The analysis technology uses near infra-red spectroscopy for material identification and compares it to a materials database. Parameters such as the calorific value, PVC content and moisture content of the solid recovered fuel are estimated in real time based on statistic data, and the process can be altered to bring the SRF in line with target specification.
The fines from both trommels join the fines line, where a magnet is first used to remove small ferrous material. The material is then mechanically divided into smaller and larger fines by a ‘flip-flop’ screen. Light fibre and plastic material is extracted by an air knife from the large fines and added to the solid recovered fuel from the oversized fraction that was separated earlier in the process. In this optical sorter, near infrared spectroscopy is used to detect molecular bonds specific to paper and plastics (not PVC). When a paper or plastic item is identified, pressurised air is fired and the item is thrown to the rear of the unit where it can be added to the solid recovered fuel material rather than lost. The rest of the material, including PVC, drops off the end of the belt.
The oversized fractions from the trommels and the heavies from the wind shifters are conveyed through a picking cabin. The picking teams manually sort material suitable for SRF production which is then added to the cleaned streams of material before a final shred.
Reflections – quality is king!
Given the nature of the site, it was no surprise to find that a number of the operational team members came from other industries where logistics and production line engineering and management are core disciplines.
Their insights and experiences have blended with the more traditional waste site team members, many who came from other SUEZ sites in the region, to get the ideal mix of appreciation, understanding and challenge to enable the cake to be suitably baked.
The same adherence to quality protocols and feedstock controls was as evident at Malpass Farm as at any other site I had been to pre-Christmas, perhaps even more so here given the nature of the plant! This site is all about producing a quality output that meets the CEMEX specification, otherwise the economics of solid recovered fuel as well as refuse derived fuel come into question. Knowledge really is power in a production facility like this.
This is a well-run site, showcased by the team winning the CIWM Team of the Year award in 2017 and SUEZ Group’s Innovation Trophy. The staff is engaged, committed and knowledgeable, being able to answer any of the questions I had about feedstock, quality, customers, problems and fuel outputs. I must say I was very impressed.
I would recommend you all see a plant like this in operation, it is a huge step forward from the days of landfill, which I can just about remember!