SUEZ site-seeing | Part 11 | Tees Valley energy-from-waste (EfW) facilities
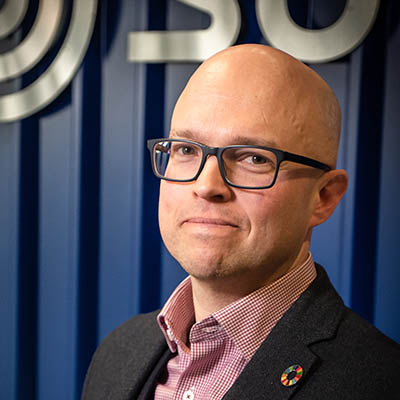
Middlesbrough is home to three SUEZ sites with a total capacity in excess of 550,000 tonnes per annum. The sites all operate independently, due to contractual requirements, but share experiences and developed local resilience in order to cover downtime and spare parts etc.
The whole site operates 24 hours a day, seven days a week, with only 10 operational staff on-site during any shift across all five lines.
Contracts, tonnages and partners
Lines one and two have been operational since 1997, they were built to service a contract with Cleveland for Middlesbrough Council, formerly known as Middlesbrough Borough Council, of 180,000 tonnes per annum. This later became a joint venture between four unitaries: Hartlepool; Stockton; Redcar and Cleveland; and Middlesbrough.
Approximately 55 tonnes a year comes from North Tyneside and unlike most of our portfolio of energy-from-waste facilities, this site is wholly owned and operated by SUEZ, rather than being part of a private finance initiative (PFI) or special purpose vehicle (SPV).
The third line is an extension to the first plant and came online in 2009 to service the Northumberland PFI contract which provides additional capacity of 136,000 tonnes per annum.
Lines four and five are contractually linked to the South Tyne and Wear PFI contract, with an additional capacity of 256,000 tonnes per annum, these lines have been in operation since 2014, with some additional waste deriving from Durham.
The technical stuff
After spending time on site across these three facilities, it is clear to see how the site has evolved, developed and learned from previous operating experience. After all the first operations date back to 1997, whilst the latest lines only kicked off in 2014.
Line three was originally restricted in design as it had to match the height of the existing lines one and two, but it has since been redesigned to enable better access to key equipment to assist with maintenance (which is perhaps the biggest lesson learned from lines one and two).
When looking at the different ‘lines’, it was clear to see that more recent upgrades on lines one, two and three, is inspired by the design and operating experiences associated with the newer lines (four and five). As many of the staff on site have worked across all of the lines, they are able to share experiences and insights to solve problems to improve the sites day-to-day operations.
Lines four and five are more advanced, given their relatively tender age. They use waste bunkers rather than a tipping floor, for a number of operational reasons and have automatic cranes to move waste from bunkers to the furnace. Lines four and five also have the largest footprint of all the lines and therefore have the most space for access and maintenance, giving this plant a much airier feel.
Ash recycling happens next door, at the Phoenix Ballast processing facility, which takes all ash from the five lines and the Kirklees plant and reprocesses it into building materials.
The energy-from-waste facility in Wilton takes residual waste from Merseyside by rail, and is only eight miles away in Redcar, North Yorkshire. I hope to be able to visit that site too in the coming months.
The technical team
A technical team was formed in 2012 after a boiler was refitted on lines one and two. This team has grown into a group of 10 professional energy engineers, who support the landfill gas and energy engineering activities at all of the SUEZ sites. Our learnings have shown that at our energy-from-waste sites the boilers are often the biggest concern, with ongoing corrosion resulting in unwanted and costly downtime. This is something that can be minimised by regular maintenance and planned refits based on the lessons learned from our existing sites.
On reflection
I must say that this is one of my favourite sites so far!
It has an iconic design, linked to Norse ships and the sea, and is one of the more colourful of our facilities which always looks good in photographs.
This is also a well-run site, a site that has shown evolution in design and process and one that is now dealing with much of the residual waste in the north east of England. It certainly doesn’t look out of place in this industrial zone just outside Middlesbrough – but don’t let the location mislead you, this site is full of passionate people, driven by quality principles (just as at our other sites) striving to meet high standards for electricity generation, and sharing its learnings across our sites for the betterment of future site designs, retrofits and refurbishments.
I had a great day on site, and learnt so much about the technologies, the costs of the kit, and the lifetime of critical equipment. A huge thanks to the team who showed me around that were very engaging and knowledgeable.