The mission
Waste prevention by reusing cardboard boxes
David Salisbury is one of the largest UK-based bespoke manufacturers of wooden orangeries, conservatories and kitchens. Over the years, the company has fully embraced environment-friendly practices. Its Highbridge factory, in fact, is considered one of the greenest manufacturing sites in the UK with features such as solar power, sustainably sourced timber, and waste and energy recycling efforts.
Driven by its commitment to the planet, the company further sought to improve its waste disposal arrangements and turned to SUEZ’s waste management expertise for support. Specifically, the company wanted to reduce landfill waste, as well as monitor and increase recycling rates, and generally ensure that all waste streams go to the best disposal options in a cost-effective manner
Our solution
Set up efficient waste management system
Among the solutions SUEZ implemented included segregating all waste streams, which meant sending all general waste to an energy-from-waste (EfW) facility, wood converted to refused derived fuel (RDF), and glass, cardboard and dry mixed recycling (DMR) materials to recycling centres.
SUEZ also monitored and weighed all types of waste. Previously, all 2.225 tonnes per week of waste went unaccounted for as majority of these went to landfill. Now, the company has a clear breakdown: 60 tonnes of wood, 35 tonnes of general waste, and 15 to 16 tonnes of cardboard/DMR – all recycled!
The overall annual waste amount remains comparable, but now it is being effectively segregated and recycled and informs the company of its recycling rates.
The results
Improved waste segregation, increased recycling, cost reduction and adoption of zero-to-landfill policy
The new waste management system implemented by SUEZ led to significant achievements including:
- Diversion of 35 tonnes of residual waste per year from landfill to energy recovery facilities.
- Increase in waste segregation and recycling by several tonnes per month.
- 100% recycling for approximately 15 to 16 tonnes of DMR annually, including previously non-recycled materials like plastics.
This enhanced set-up aligns perfectly with the waste hierarchy, prioritising more sustainable practices like recovery and recycling over disposal. It also ensures cost-effectiveness by finding the best disposal options for each waste stream
35
tonnes
of waste diverted from landfill to energy
15-16
tonnes
of DMR recycled annually
We have seen reduced costs, reliable service and improved employee engagement as we now recycle 100%. I definitely would recommend SUEZ.Stephen Carpenter , Head of Health & Safety and Environment, David Salisbury
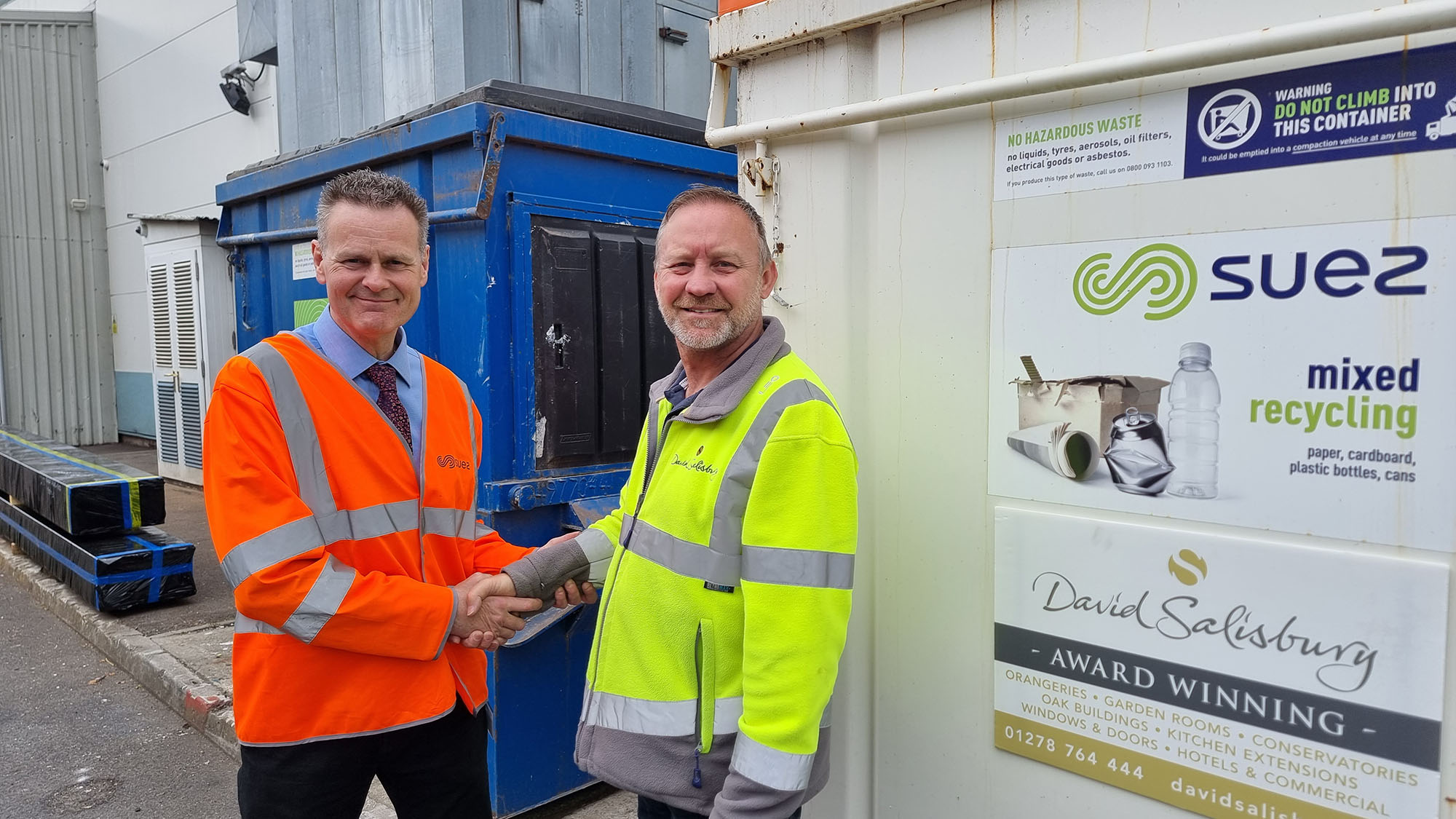